Willkommen bei Autocodierungen.de
Ihr unabhängiger Ratgeber für Autocodierung, OBD-Systeme und Fahrzeugdiagnosesoftware
Finden Sie die besten Produkte und Dienstleistungen für Ihr Fahrzeug
- Handverlesene Angebote
- Expertenbewertungen
- Unabhängige Beratung
Expertise
Auswahl
Wir helfen Ihnen dabei, die beste Auswahl zu treffen. Unsere unabhängigen Ratgeber bieten Ihnen eine präzise Analyse der besten Produkte und Dienstleistungen auf dem Markt.
Vertrauen
Vertrauen ist unser Grundprinzip. Wir bieten Ihnen zuverlässige Beratung und echte Bewertungen, damit Sie die richtige Wahl treffen können.
Expertenrat und aktuelle Neuigkeiten
Hier finden Sie Tipps, Tricks und Ratgeber zu Autocodierung und Diagnosesoftware für verschiedene Fahrzeugmarken.
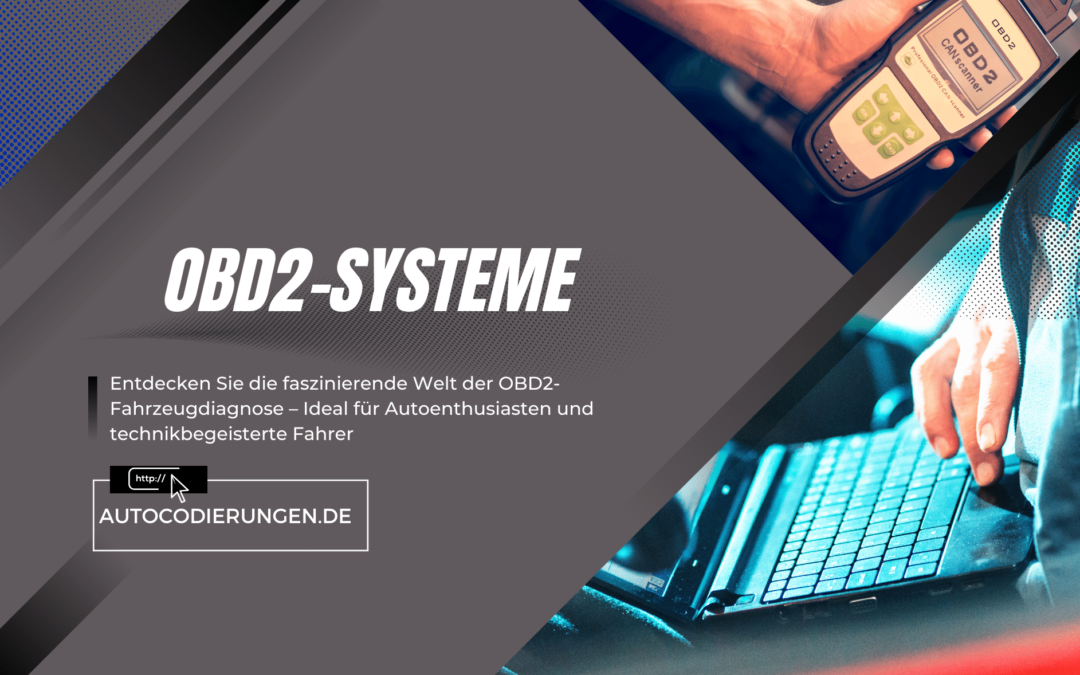
OBD2-Systeme: Revolution der Fahrzeugdiagnose?
Haben Sie sich jemals gefragt, wie Ihr Auto 'denkt' und sich selbst überwacht? Das OBD2-System ist das Gehirn hinter dieser faszinierenden Technologie. Aber was kann es wirklich leisten? Die Evolution der Fahrzeugdiagnose Willkommen in der Welt der modernen...
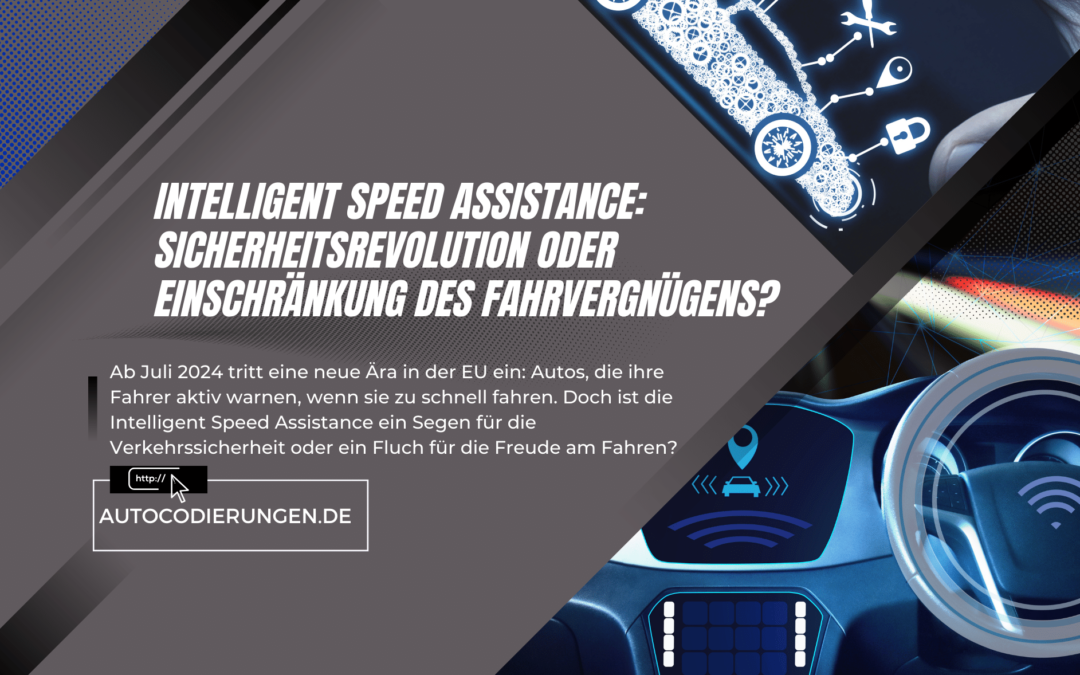
Intelligent Speed Assistance ab 2024: Sicherheitsrevolution oder Einschränkung des Fahrvergnügens?
Ab Juli 2024 tritt eine neue Ära in der EU ein: Autos, die ihre Fahrer aktiv warnen, wenn sie zu schnell fahren. Doch ist die Intelligent Speed Assistance ein Segen für die Verkehrssicherheit oder ein Fluch für die Freude am Fahren? Während die ISA-Technologie das...
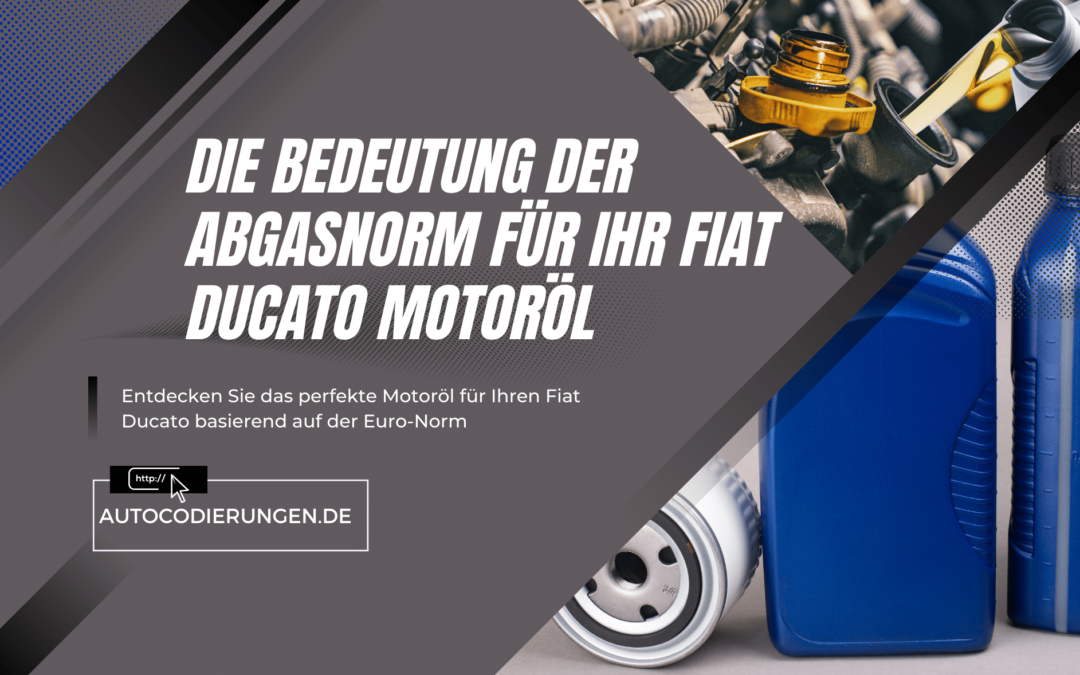
Die Bedeutung der Abgasnorm für Ihr Fiat Ducato Motoröl
In der Welt der Nutzfahrzeuge spielt der Fiat Ducato eine tragende Rolle. Er ist nicht nur ein treuer Gefährte im Gewerbe, sondern auch ein verlässlicher Begleiter für Reisemobile. Um die Beständigkeit und Effizienz Ihres Ducatos zu gewährleisten, ist die Wahl des...
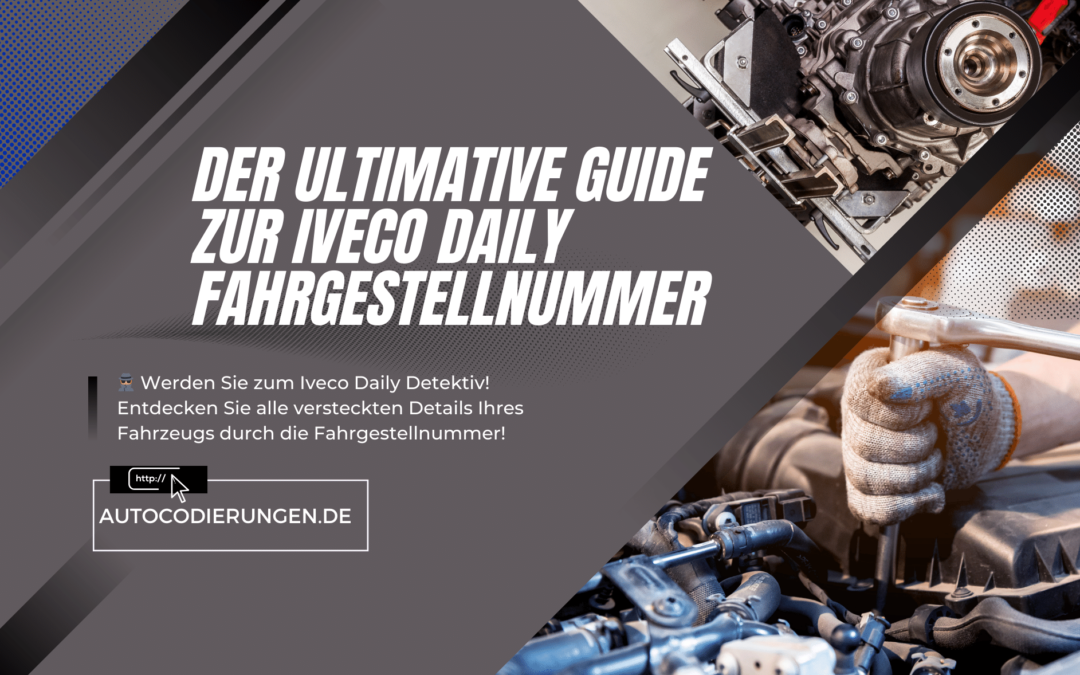
Der ultimative Guide zur Iveco Daily Fahrgestellnummer
Die Fahrgestellnummer, auch bekannt als Fahrzeugidentifikationsnummer (VIN), ist weit mehr als eine zufällige Kombination von Zeichen. Sie ist wie der Fingerabdruck Ihres Iveco Daily – einzigartig und individuell zugeschnitten auf Ihr Fahrzeug. Sie enthält eine...
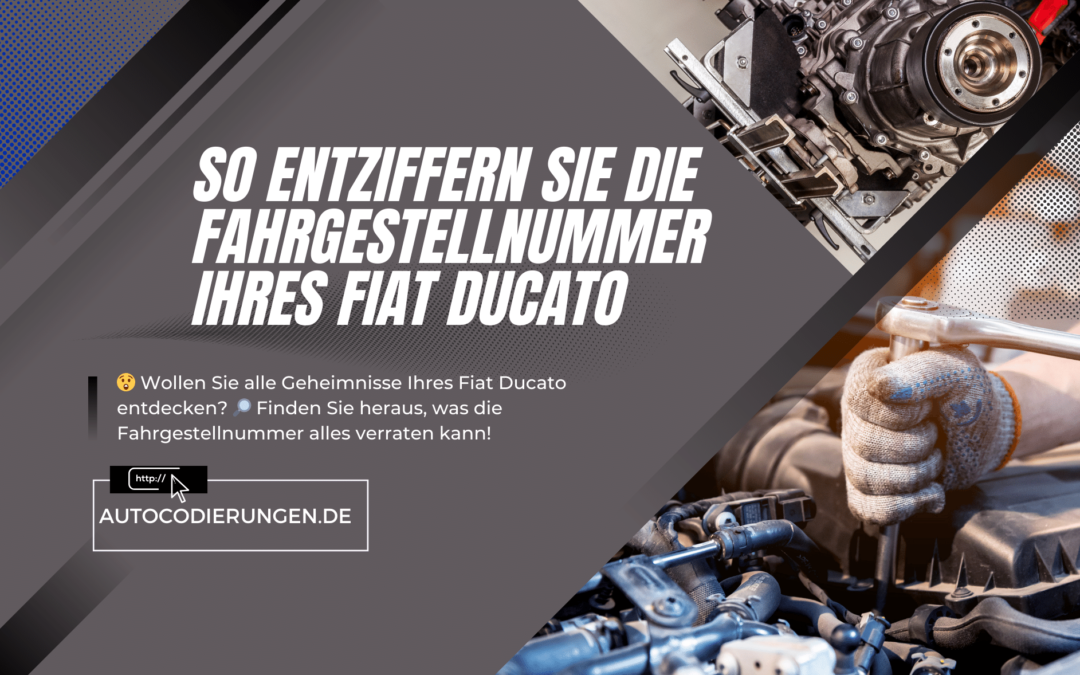
So entziffern Sie die Fahrgestellnummer Ihres Fiat Ducato
Sie sind stolzer Besitzer eines Fiat Ducato, ein Fahrzeug, das durch seine Zuverlässigkeit und Vielseitigkeit besticht. Doch haben Sie sich jemals gefragt, was die mysteriöse Folge von Zahlen und Buchstaben auf Ihrem Fahrzeugschein oder im Motorraum Ihres geliebten...
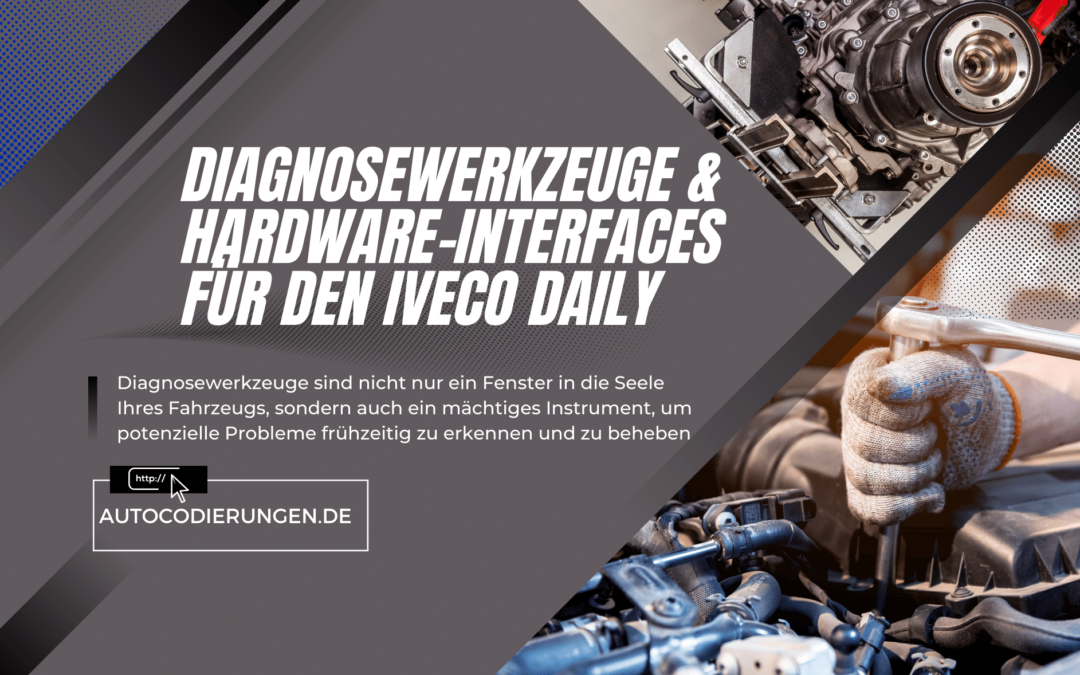
Diagnosewerkzeuge und Hardware-Interfaces für den Iveco Daily
Willkommen zu unserem umfassenden Leitfaden über Diagnosewerkzeuge und Hardware-Interfaces speziell für den Iveco Daily. Hier teilen wir unser gebündeltes Wissen mit Ihnen, um Ihnen den Weg zur effektiven Nutzung dieser Werkzeuge aufzuzeigen. Kurze Einführung in die...
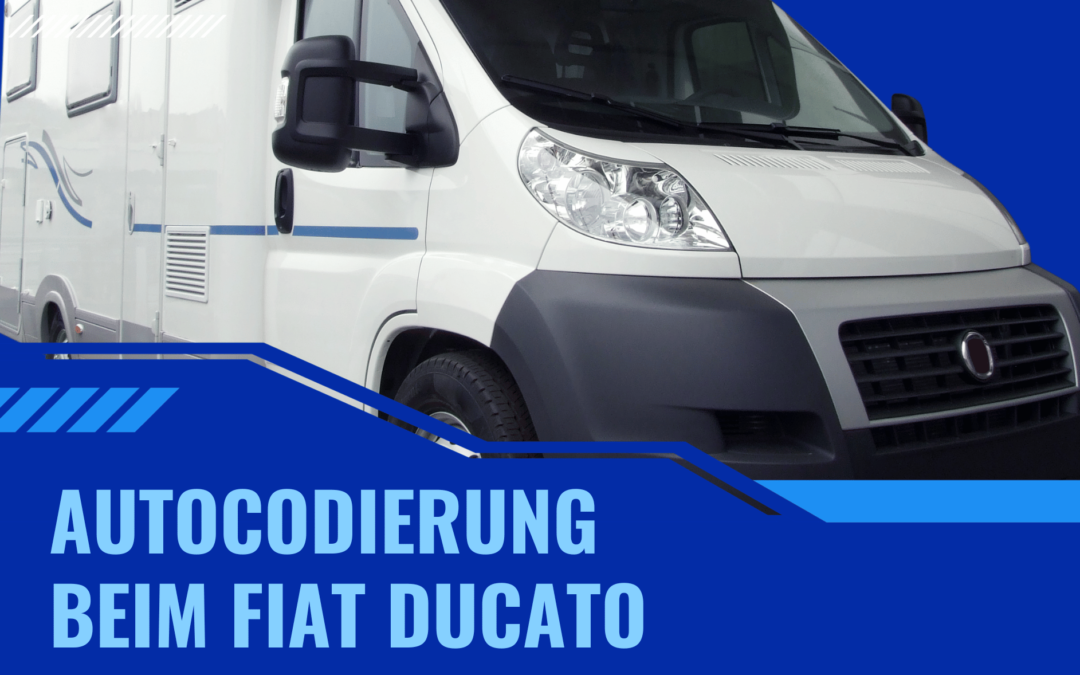
Autocodierung beim Fiat Ducato
Einleitung: Die Revolution der Fahrzeugdiagnose In der rasant fortschreitenden Automobilwelt steht uns nun eine Revolution bevor, die den Besitzern eines Fiat Ducato das Leben erleichtern wird. Dank der innovativen Kombination aus Multiecuscan Fahrzeugdiagnosesoftware...
Über Uns
In der rasant wachsenden Automobilindustrie ist es unerlässlich, über die neuesten Entwicklungen und Technologien auf dem Laufenden zu bleiben. Autocodierungen.de ist Ihr zuverlässiger Ratgeber, der Ihnen hilft, die Komplexität der Autocodierung, OBD-Systeme und Fahrzeugdiagnosesoftware zu entwirren.
Durch unsere unabhängige Beratung unterstützen wir Sie dabei, fundierte Entscheidungen zu treffen und das Beste aus Ihrem Fahrzeug herauszuholen. Ob Sie ein erfahrener Mechaniker oder ein Autoenthusiast sind, unsere Experten-Ratgeber bieten Ihnen umfassende Informationen und Bewertungen zu den neuesten Produkten und Dienstleistungen in der Branche.
Vertrauen Sie auf unsere Expertise und navigieren Sie sicher und informiert durch die Welt der Autocodierung.